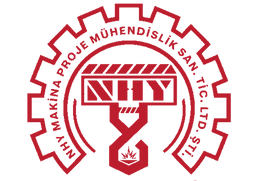
Cooling Cabinet
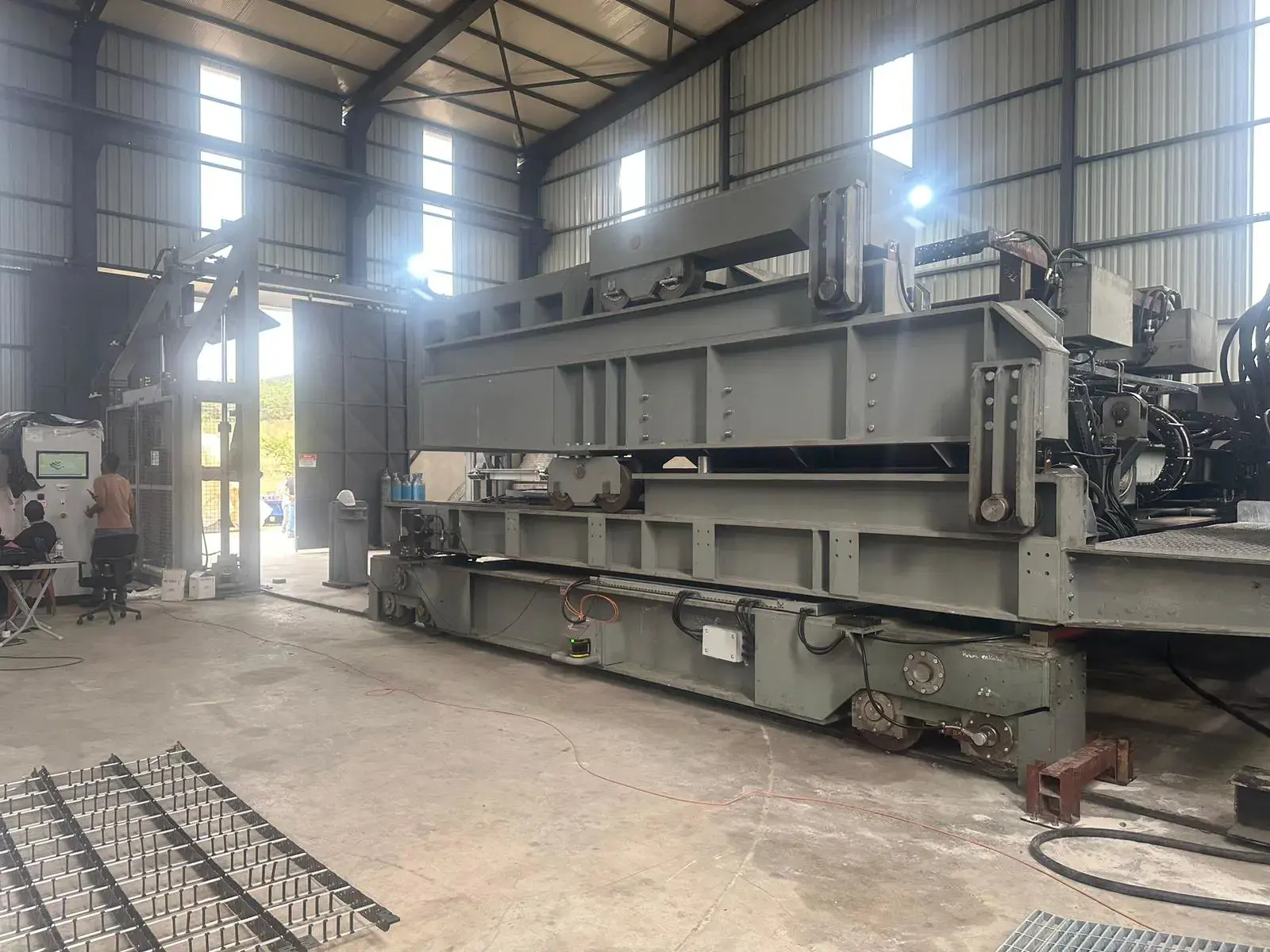
Cooling Cabinets Metal cases made for use in the cooling industry are called cooling cabinets. There is a strong cooling chassis at the bottom of the cabins. In Which Sector Are Cooling Cabinets Used? It is designed for use in the heating and cooling area. It is especially used in the cooling industry. What is the Structure of Cooling Cabinets? It is a work containing metal. The lower chassis part is made of slightly more durable material. Some places are gated and secured with locks.
The whole structure is positioned on this chassis. So much so that it can change the shape,
size and even design of the cabin to be designed based on the location of the engine, radiator and filter.
Air intake and air discharge areas have been specially designed and heating elements have been removed.
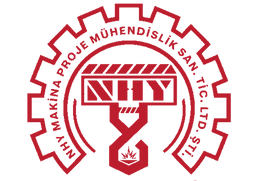
Homogenization and Cooling System
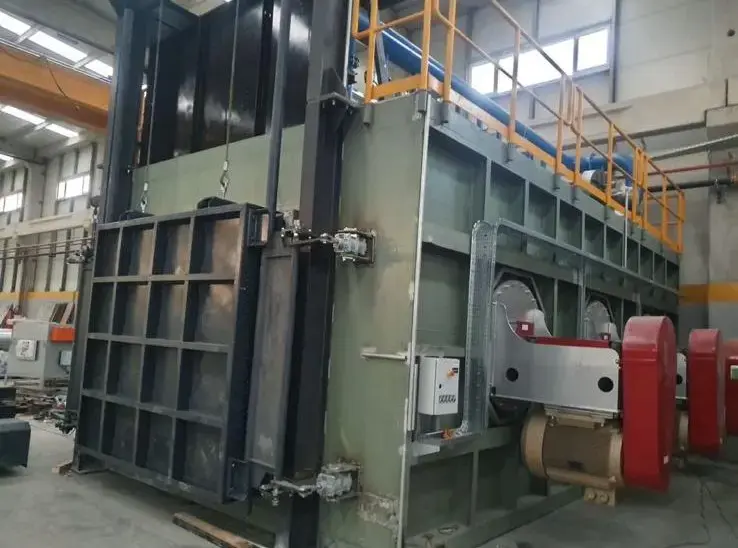
Homogenization Oven; It is designed for the homogenization of aluminum billets produced in different diameters.
These are heat treatment furnaces used to improve the mechanical properties of metal.
The desired capacity is designed and manufactured in accordance with the fuel type. General features of aluminum that make it preferred in the industrial field: density,
chemical stability, aesthetic properties, strength, flexibility, processability and conductivity.
Material stability must be ensured in producing the final product that has all of these features. In continuous casting,
rapid heat conduction prevents the equalization of alloying elements in grains with different structures,
so supersaturation and grain segregation are higher than in slow-cooled gravity casting. Supersaturation and grain separation in the material can only
be eliminated by good homogenization.
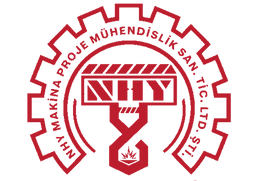
Crushing and Screening Plant
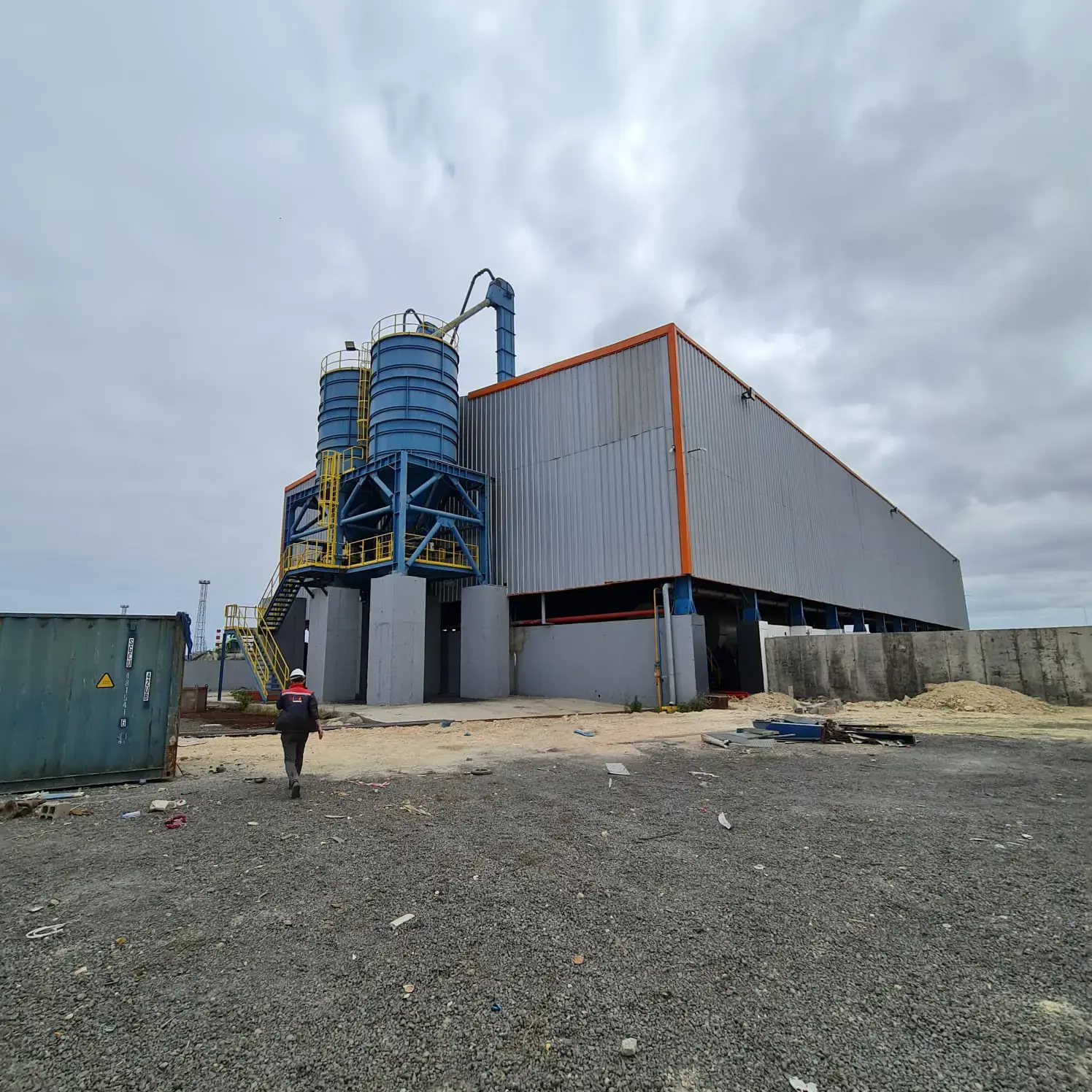
Crushing and screening facilities are used to separate stones of different hardness into desired sizes; It is a facility consisting of feeders, crushers,
screens and belts. These facilities are used to produce aggregates to be used in constructions, highways, railways,
asphalt and concrete plants. Fixed crushing and screening plants are used for continuous and very long projects,
and mobile crushing and screening plants are used for smaller and short-term projects. Another name for crushing,
screening and washing facilities is crushing facilities. The Crushing and Screening process generally consists of 4 parts. 1- Rough Crushing Process After the material to be crushed is unloaded by the truck, it is loaded homogeneously into jaw and primary crushers by the feeder,
and the crushing process is carried out to reduce the largest stones to one size smaller. The crushed material is carried to other crushers by belts. 2- Medium and Fine Size Crushing Process After the materials resulting from the first crushing process are sieved through the sieve,
they are transported to the secondary crusher and jaw crusher with a belt conveyor for the crushing process. The crushed stones are sent to the
sieve via the belt conveyor and materials of various sizes are separated. 3- Smallest Material/Sand Making The crushed stones are sent to a conical,
vertical shaft or impact crusher (sand making machine) for further crushing and shaping and are turned into the smallest size. Step 4: Washing Finely ground and shaped materials are sieved with the help of a sieve for coarse, medium and fine sand. If clean aggregate is desired,
it is sent to the sand auger and the washing process is carried out.
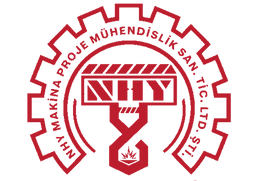
Aluminum Casting Plant
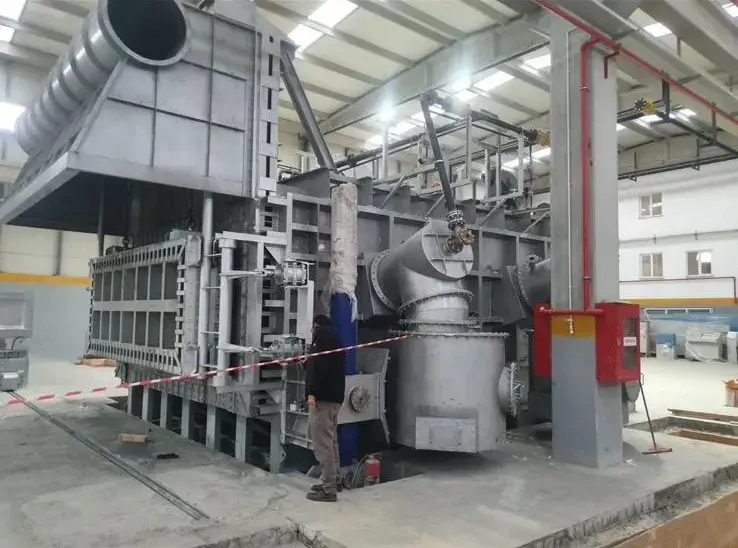
In tilting reverberatory type furnaces, raw materials (ingots, ingots and intermediates) are melted up to a certain temperature for certain periods of time.
After the desired tonnage is ready, a sample is taken from the homogeneously mixed liquid metal and its chemical composition values are determined on
the Arl Metal Analyzer spectrometer device. Alloying process (SI, Mn, Mg, Cu, Mn, Cr) is performed on the liquid metal until the chemical composition is obtained.
After the desired alloy content is obtained, the pre-refining process is completed by cleaning the slags along with the degassing process in the liquid aluminum
by using a special method, Slag forming flux, together with nitrogen gas. The liquid metal, which is ready for casting in terms of temperature and analysis,
passes through the runner and reaches the casting table after passing through the Sıvex Lp Grade 40 filter. Casting parameters (casting speed, water flow rate,
water temperature, metal temperature, etc.) are entered using the PLC program and casting begins. Billets are produced in the diameters requested by the customer.